现场改善 - NPS新生产技术与传统生产方式
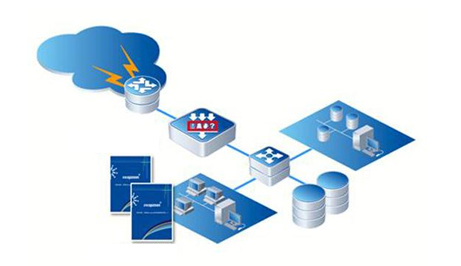
1、 NPS的由来: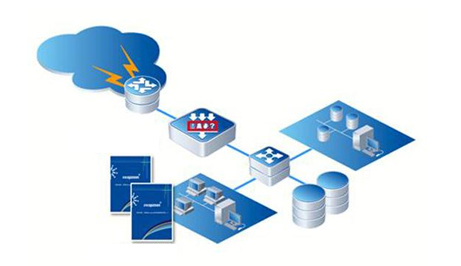
为突破生产困境,改变传统的生产型态,而产生了“新生产技术”(New Production Skills)。
2、NPS的起源:
NPS是导源于日本的丰田生产方式,或是一般所称的“及时生产”(Just-In-Time)方式。由早期与丰田生产方式的创始者大野耐一一起开发、实施的一群人,将其内涵及应用范围加以改进,而推广应用于汽车业以外的许多不同规模有行业的新型生产方式。
3、具体内容心、技、体:
“心”即表示思想观念的改变,NPS的思想与传统的生产观念有很大的不同,必须先从事意识改革。
“技”即表示技法的意思,就是要应用什么样的技法,才能表达出思想。就技法而言,可分成四个招式,
第一招是“流线化生产”,
第二招是“安定化生产”,
第三招是“平稳化生产”,
第四招是“超市化生产”。
“体”即表示体验、实践的意思。
4、建立全体员工共识:
A、 对全公司的所有员工,从最高领导者一直到现场基层干部进行教育,使全体员工认识市场型太的演变、新生产技术的思想、达成共识;
B、对NPS有坚强的信念;
C、将有信心及信念扔员工组成“自主研究会”,选定示范生产线,来证明它的卓越成果。
4、NPS与传统生产方式的差异
(1)改善
NPS的改善见解,是超乎一般人的认识。改善,顾名思义就是改变为良善之意,所以关键要能改变,如果一切都保持与以往一样的做法,当然看不到改善的成果。其次要变得更良善,其意是指要能以更少资金投入成本,来取得更良善的结果。例如:能用200元的成本投入,达成节省材料耗用量,却花了10万无,才达成相同的效果,这不叫改善,而是浪费了。所以,NPS对改善的做法强调如下:
a、改善并不是专业工程师的工作,是每一个人都必须而且也有能力参与的工作。同时,要能运用正确的生产思想观念来进行改善,不要在传统的生产思想里打转。
b、改善的活动要以课题为导向,加于定期化、制度化,组成跨部门的小集团,采取任务性编组,来完成改善的课题。目标达成后,改善小组就可解散。
c、要持续性、小步伐地逐步改善,以最小的资金成本,现状为基础,先从作业改善做起,一小步、一小步地达成目标,随着时间的进展,终于产生大幅度的进度效果。
d、改善强调的是要运用公司内部人员的智慧及创意,来达成改善的目标。如果是花钱从外面买进现成的技术或设备来达成目标,那便是别人的改善,而不是自己的。
(2) NPS与传统生产方式的差异
改善要运用新的生产思想观念才能得到突破,产生大效果。如果仍然抱残守缺,在传统的观念下做改善,不但效果有限,有时走错了方向还不知道。所以要改善就必须了解、学习、运用NPS新生产技术的思想观念。因为NPS强调的生产思想观念,与传统的观念完全不同。
a、传统生产方式
以生产者为中心,一切的生产理念与做法,都是以自己的方便性为思考的出发点。为了减少换模时间的损失,而喜好采用依据预测需要,计划地大批量生产,建立成品库存来等待顾客下订单。这种方式,表面上赢得了所谓生产效率的发挥,却埋下了库存过多,管理负荷增加,总体成本增加,库存品过时降价报废的危险,而陷企业于危机中。
b、NPS新生产方式
以消费者为中心,不建立成品库存为努力的目标,采用接单生产。依据订单的型式、数量及交期,在必要的时间,生产出必要数量之必要型式的产品,亦即变种变量生产模式。不管多种少量,或是少种大量,皆应付自如。因此,缩短换模时间是必要的,也因而衍生出了
许多如下表格所示不同的实践方法。
(1)心、技、体结合,体系完整
有些改善管理方式谈了许多理论及思想、但缺乏实践理论及技术,以及如何实践出来的行动。理论再好,技法再佳,如果没有实践出来,结果还是一场空。NPS的整个体系相当完整,它提出了与传统生产观念不同的新思想观念(心),以及实现此观念的技法(技)和实践(体)此理想境界的“自主研究会”改善小组的活动方式,此即“知行合一”的实现。
(2)追求全方位的成果
NPS的改善目标明确且全面性。它可以达成:提高劳动生产力、减少不良品数量、缩短生产交货期、降低仓库库存量、节省空间的需求、减少人力的需求及创造企业的利润。
(3)一点切入,万流归宗
NPS改善的另一个特点是不管改善的主题是哪一类别的主题,或由哪一类的主题做起,但最后均能产生上述全方位的成果。例如:以提升劳动生产力为改善的主题作为出发点,最后成果也可以看到不良率降低了,在制品库存减少了,生产交期变快了,生产空间节省了等等。这与传统的改善效果完全不同,而且快速地达成目标。
TPM,点检,班组建设,管理能力咨询培训@左明军老师.微信:13808969873