TPM改善 - 以“秒”为单位细致改善的规则
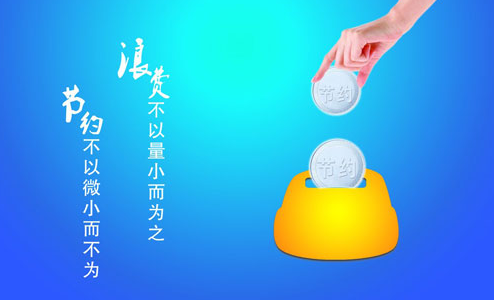
依照生产线平衡的思想和动作经济的原则,生产率会提高1倍
第一次的作业只是以瓶颈工序为中心,改善了生产线平衡状况,可以预测到生产效率大约提高了30%。 第2次作业时,作业人员人数相同,只是更换作业的内容,对发现的地方加以改善,其纯作业时间变成了如下状况:
1工序(30秒)、2工序(26秒)、3工序(26秒)4工序(33秒)、5工序(26秒)、6工序(20秒)第2次的平衡损失率大约为18.7U/o,即使是以生产线平衡为中心,也改善了11.1%。 因为产出速度( pitch time)是35秒,所以生产效率提高了29u/o,基本上得到了预想的结果。
接着,考虑动作经济的原则,以秒为单位进行动作分析,第3次的纯作业时间变成了如下状况:
1工序(19.5秒)、2工序(24秒)、3工序(24秒)4工序(10.5秒)、5工序(23.5秒)、6工序(19.7秒)平衡损失率大约为8.9010,20.9%得到了改善。 似乎只要看见被拍摄进VTR里的作业,就还能发现作业的浪费,也就有进一步改善的余地。
这样,如果知道以秒为单位细致看问题的方法和改善的规则,就能够很容易发现浪费,然后可以运用丰田“7种浪费”等消除浪费的思想进一步改善。
二、改善的规则
(一)丰田的7种浪费
丰田生产方式认为,不产生附加价值的一切作业都是浪费,它把浪费分为以下7种。
1.生产过剩的浪费
一心想要多销售而大量生产,结果在人员、设备、原材料方面都产生浪费。在没有需求的时候提前生产而产生浪费。
2.不合格产品的浪费
在生产过程中出现废品、次品,会在原材料、零部件、返修所需工时数、生产这些不合格产品所消耗的资源方面产生浪费。
3.待工的浪费
在进行机械加工时,机器发生故障不能正常作业,或因缺乏零部件而停工等活等,在这样的状态下所产生的浪费都是停工等活的浪费。
4.动作上的浪费
不产生附加价值的动作、不合理的操作、效率不高的姿势和动作都是浪费。
5.搬运的浪费
除去准时化生产所必需的搬运,其他任何搬运都是一种浪费。比如在不同仓库间移动、转运、长距离运输、运输次数过多等。
6.加工本身的浪费
把与工程的进展状况和产品质量没有任何关系的加工当做是必要的加工而进行操作,此种状况下所产生的浪费。
7.库存的浪费
因为原材料、零部件、各道工序的半成品过多而产生的浪费。这些东西过度积压还会引起库存管理费用的增加。
(二)消除7种浪费的步骤
从哪里开始消除这7种浪费为好呢?在像丰田一样积累了50年以上的改善经验和没有这些改善经验的企业中,在生产体制上存在着很大差异。 在此让我们以问题比较多的企业为对象,来思考一下处理7种浪费的基本顺序。
步骤①:
在需要的时候适时生产需要的产品可以排除生产过剩的浪费,这需要具备严格管理的思想。
步骤②:
如果经常产生不合格产品,抑制生产过剩是很困难的。我们要消除不合格产品,消除制造不合格产品的浪费。
步骤③:
对于停工等活,只要明白其要点就很容易改善。消除停工等活的浪费,有效利用人力资源。
步骤④~⑥可以根据消除浪费的着眼点从可以实施的部分开始实施。
步骤④:
对于动作的浪费,如果减少工时数(人数×时间)将会对消除浪费产生很大影响。但是,即使是进行动作分析,清除了一些细小的浪费,也会被其他的问题所掩盖,所以必须注意。
步骤⑤:
要消除搬运的浪费,就要在搬运距离和搬运次数等方面加以改进。
步骤⑥:
对于加工过程中本身的浪费,要认识到不产生附加价值的一切东西都是浪费。
步骤⑦:
如果按照①~⑥步骤操作,库存必然会减少。虽然这些问题堆积如山,但是如果追求库存为零将会产生许多问题。根据企业的水平,最好在最后阶段消除库存的浪费。
浪费 | 内容 | 原因 | 对策 |
生产过剩的浪费 |
①生产过多 ②生产过早 ③妨碍生产流程 ④成品库存、半成品库存增加 ⑤资金周转率低下 |
·与顾客交流不充分 ·依赖个人经验和思维方式制订的生产计划 ·人员过剩·设备过剩·大批量生产 ·生产负荷变动 ·在生产过程中产生问题(如产生不合格产品、发生机械故障等) ·生产速度提高 |
·与顾客充分沟通 ·生产计划标准化 ·均衡化生产 ·一个流程 ·小批量生产 ·灵活运用看板管理技术组织生产 ·快速更换作业程序 ·引进生产节拍(tact time) |
不合格产品的浪费 |
①原材料的浪费②开动率低下 ③检查的浪费 ④用户索赔而引起的企业信用低下 ⑤库存增加 ⑥再生产的浪费 |
·对于可能产生不合格产品的意识薄弱 ·在生产过程中不注重产品质量 ·检查中心的管理检查标准不完善(特别是功能检查) ·教育训练体制不健全、顾客对于产品质量要求过多、缺乏标准作业管理 |
·产品质量是在工序中创造的 ·坚持贯彻自动化、现场、现货、现实的原则 ·制订培养相关意识的对策 ·通过不断问“为什么”的对策,防止问题再次发生 ·引进预防错误的措施 ·确立产品质量保证体制 ·使改善活动与质量体系(ISO9001)有效融合 |
待工的浪费 |
①在反复作业的过程中,标准作业管理不完善 ②监视 ③表面作业 ④停工等活 ⑤机器设备、人员等有富余 |
·生产工序流程不合理 ·前道工序和后道工序产生了问题 ·停工等活、等料待工 ·表面作业 ·设备配置不合理 ·在生产过程中的作业能力不平衡 ·大批量生产 |
·引进均衡化生产、生产节拍的概念 ·努力使生产工序流程合理,发现浪费 ·U字形配置 ·快速更换作业程序 ·再分配作业 ·禁止停工等活时的补偿作业 ·生产线平衡分析 ·认清表面作业 ·安装能够自动检测到异常状况并且自动通知异常状况的装置 |
动作上的浪费 |
①不产生附加价值的动作 ②生产率低下的动作 |
·机器与人的作业不明确 ·毫无意识地实施了不产生附加价值的动作 ·生产布局不合理 ·培训不充分 |
·生产工序流程化 ·U字形设备配置 ·对生产率低下的动作加以培训,并且贯彻落实 ·善于发现和消除表面作业 ·活用标准作业组合表 ·根据是否会产生附加价值研究相应对策 |
搬运的浪费 |
①在不同的仓库间移动产品和转运 ②空车搬运 ③搬运的产品有瑕疵 ④空间的浪费使用 ⑤搬运距离和搬运次数 ⑥增加搬运设备 |
·欠缺“搬运和寻找不是工作”这一观念 ·生产布局不合理 ·活性指数低 ·与生产顺序组合时,研究商讨不足 |
·培养不要搬运的观念 ·确定最佳搬运次数 ·U字形设备配置 ·小容量化 ·活用各种搬运方式(豉虫搬运方式等) ·成套搬运零件 ·提高活性指数 |
加工本身的浪费 |
①为不必要的工序和不需要的作业增加人员和工时数 ②生产率低下 ③次品增加 ④按照过去的习惯操作,不加改善 |
·生产工序设计不合理 ·作业内容分析不足 ·对人和机器功能的分析不完全 ·处理异常停止的对策不完善 ·TPM不完善 ·夹具工具不完善 ·标准化体制不完善 ·员工技术不熟练·缺乏原材料 |
·改进以往习惯操作方式 ·解决现场主义问题 ·研讨检查方法·使生产工序设计合理化·运用夹具工具 ·人工智能化(引进机器人) ·生产自动化 ·贯彻标准作业 ·研讨原材料对策 ·完善设备故障经验处理方案 ·培养技术熟练的TPM作业人员 |
库存的浪费 |
①成品、半成品库存积压 ②库存管理费用(仓库和搬运设备的折旧费、维修费、搬运费、税金、保险费、投资利息、损耗费、老化费等) ③产生库存是掩饰过多问题的结果 |
·均衡化生产体制不健全 ·多准备些库存是交货期管理(出货准备)所必需的意识 ·设备配置不合理 ·大批量生产 ·提前生产 ·在等活时产生的富余生产人员 |
·与顾客充分沟通 ·培养针对库存的意识(只生产能销售的产品) ·生产工序流程化 ·贯彻看板体制,将物品和信息一并运送 ·使生产工序中的问题无限接近为零 |
TPM,点检,班组建设,管理能力咨询培训@左明军老师.微信:13808969873